- +1.801.556.9254
- chad.adams@mach9solutions.com
- 8:30 - 17:00 (MST)
Our 3 Step Development Process
We work hard with our customers to create trusted partnerships and help them minimize the waste created from poor measurement systems
Tooling/Fixture
Design
- Initial Fixture Concepts Developed
- Customer Design Review & Approval
- Final Detailed Design Completed
- Second Design Review with Customer (if Requested)
- Release for Fabrication
Fabrication &
Assembly
- Order Raw Materials
- Mill / Turn / 3D Print / Fabricate Components
- Pre-assemble & Run Preliminary Gage R&R
- Send out For Finishing (anodizing, plating, etc.)
- Final Assembly and Inspection
Qualification,
Delivery & Support
- Develop Measurement Procedure & Test Protocol
- Deliver Fixture to Customer’s Site
- Train Operators on the Procedure
- Perform Final Gage R&R at Customers Site
- Final Approval From Customer
If your Proof of Concept, Design Verification, Validation, Reliability, Manufacturing / QC Inspection Test Systems Perform Like This...
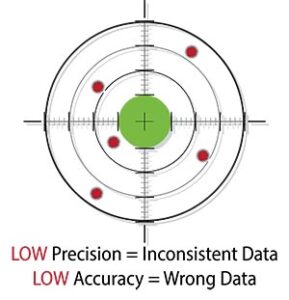
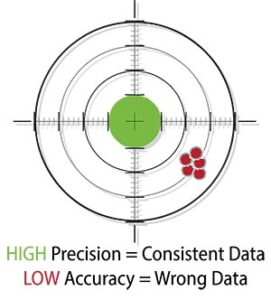
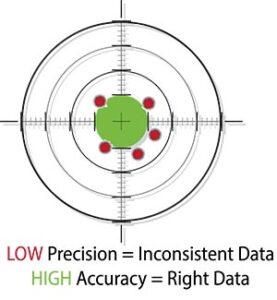
Then You Will Recognize the Impact it’s Having on your Business Performance...
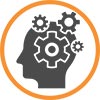
Research & Development
• Unpredictable and inconsistent product performance
• Unplanned and expensive “design – build – test cycles”
• Long and unpredictable development time lines
• Missed launch date commitments
• Poor post design transfer product quality and performance
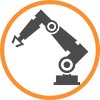
Process Development
• Poor process stability
• Inadequate short and long term process capability
• Tight process windows requiring extra product sampling, testing and machine adjustments to stay in control
• Repeated and unplanned IQ, OQ and PQ test runs to meet acceptance criteria
• Additional components and cost from repeat testing
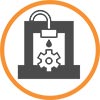
Manufacturing Engineering
• Unnecessary product testing that impacts yield and productivity
• Needless cost variance from ship holds, scrap, and product dispositions created from bad test data
• Confounded root cause analysis that impedes continuous improvement activities
• Poor equipment availability from frequent line stops due to subassembly testing
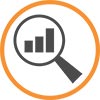
QA & Test Management
• Large volumes of unnecessary corrective and preventative action plans
• Unnecessary product performance testing
• Needless ship holds, scrap, and product dispositions from bad test data
• Increased Regulatory audit finding risk
• Needless training and inspection procedures
Partnering with us to develop your fixtures and automated test systems will help eliminate precision and accuracy bias so you can stay focused on what you do best. Delivering high performing and high quality products to your customers while improving your businesses performance!
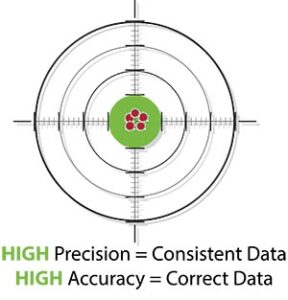